ഷെൽ മോൾഡ് കാസ്റ്റിംഗ്ഒരു തെർമോസെറ്റിംഗ് റെസിൻ കലർന്ന മണൽ ചൂടാക്കിയ മെറ്റാലിക് പാറ്റേൺ പ്ലേറ്റുമായി സമ്പർക്കം പുലർത്താൻ അനുവദിക്കുന്ന ഒരു പ്രക്രിയയാണ്, അങ്ങനെ പാറ്റത്തിന് ചുറ്റും പൂപ്പലിൻ്റെ നേർത്തതും ശക്തവുമായ ഒരു ഷെൽ രൂപം കൊള്ളുന്നു. തുടർന്ന് പാറ്റേണിൽ നിന്ന് ഷെൽ നീക്കം ചെയ്യുകയും കോപ്പും ഡ്രാഗും ഒരുമിച്ച് നീക്കം ചെയ്യുകയും ആവശ്യമായ ബാക്ക്-അപ്പ് മെറ്റീരിയലുമായി ഒരു ഫ്ലാസ്കിൽ സൂക്ഷിക്കുകയും ഉരുകിയ ലോഹം അച്ചിൽ ഒഴിക്കുകയും ചെയ്യുന്നു.
സാധാരണയായി, കളിമണ്ണിൽ നിന്ന് പൂർണ്ണമായും സ്വതന്ത്രമായ വരണ്ടതും നേർത്തതുമായ മണൽ (90 മുതൽ 140 GFN വരെ) ഷെൽ മോൾഡിംഗ് മണൽ തയ്യാറാക്കാൻ ഉപയോഗിക്കുന്നു. തിരഞ്ഞെടുക്കേണ്ട ധാന്യത്തിൻ്റെ വലുപ്പം കാസ്റ്റിംഗിൽ ആവശ്യമുള്ള ഉപരിതല ഫിനിഷിനെ ആശ്രയിച്ചിരിക്കുന്നു. വളരെ സൂക്ഷ്മമായ ഒരു ധാന്യ വലുപ്പത്തിന് വലിയ അളവിൽ റെസിൻ ആവശ്യമാണ്, ഇത് പൂപ്പൽ ചെലവേറിയതാക്കുന്നു.
ഷെൽ മോൾഡിംഗിൽ ഉപയോഗിക്കുന്ന സിന്തറ്റിക് റെസിനുകൾ അടിസ്ഥാനപരമായി തെർമോസെറ്റിംഗ് റെസിനുകളാണ്, അവ താപത്താൽ മാറ്റാനാവാത്തവിധം കഠിനമാക്കുന്നു. ഏറ്റവും വ്യാപകമായി ഉപയോഗിക്കുന്ന റെസിനുകൾ ഫിനോൾ ഫോർമാൽഡിഹൈഡ് റെസിനുകളാണ്. മണലുമായി സംയോജിപ്പിച്ച്, അവർക്ക് വളരെ ഉയർന്ന ശക്തിയും ചൂടിൽ പ്രതിരോധവുമുണ്ട്. ഷെൽ മോൾഡിംഗിൽ ഉപയോഗിക്കുന്ന ഫിനോളിക് റെസിനുകൾ സാധാരണയായി രണ്ട് ഘട്ടങ്ങളുള്ളവയാണ്, അതായത്, റെസിനിൽ അധിക ഫിനോൾ ഉണ്ട്, കൂടാതെ ഒരു തെർമോപ്ലാസ്റ്റിക് മെറ്റീരിയൽ പോലെ പ്രവർത്തിക്കുന്നു. മണൽ പൂശുമ്പോൾ, തെർമോസെറ്റിംഗ് സ്വഭാവസവിശേഷതകൾ വികസിപ്പിക്കുന്നതിനായി റെസിൻ ഏകദേശം 14 മുതൽ 16% വരെ അനുപാതത്തിൽ ഹെക്സ മെത്തിലീൻ ടെട്രാമൈൻ (ഹെക്സ) പോലുള്ള ഒരു ഉൽപ്രേരകവുമായി സംയോജിപ്പിക്കുന്നു. ഇവയ്ക്കുള്ള ക്യൂറിംഗ് താപനില ഏകദേശം 150 C ആയിരിക്കും, ആവശ്യമായ സമയം 50 മുതൽ 60 സെക്കൻഡ് വരെ ആയിരിക്കും.
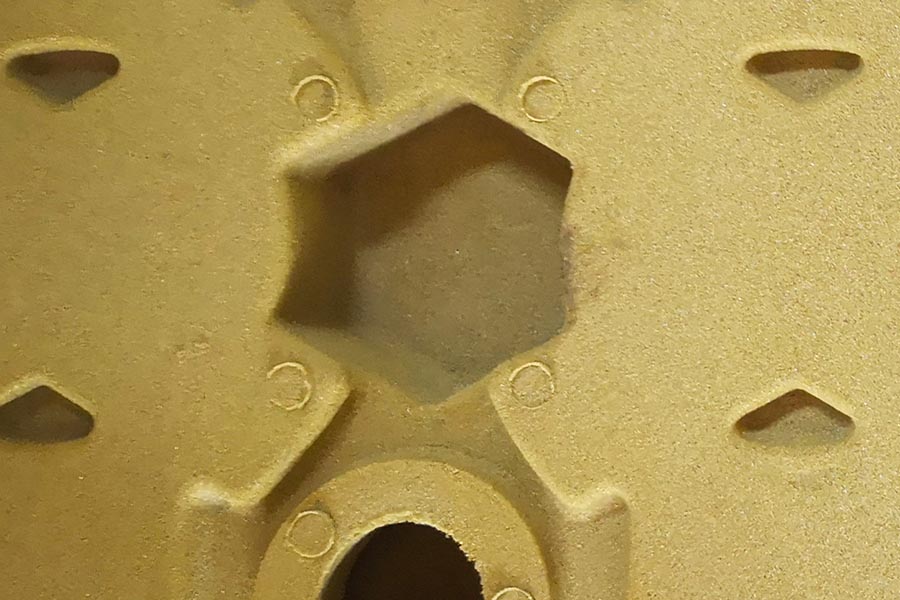
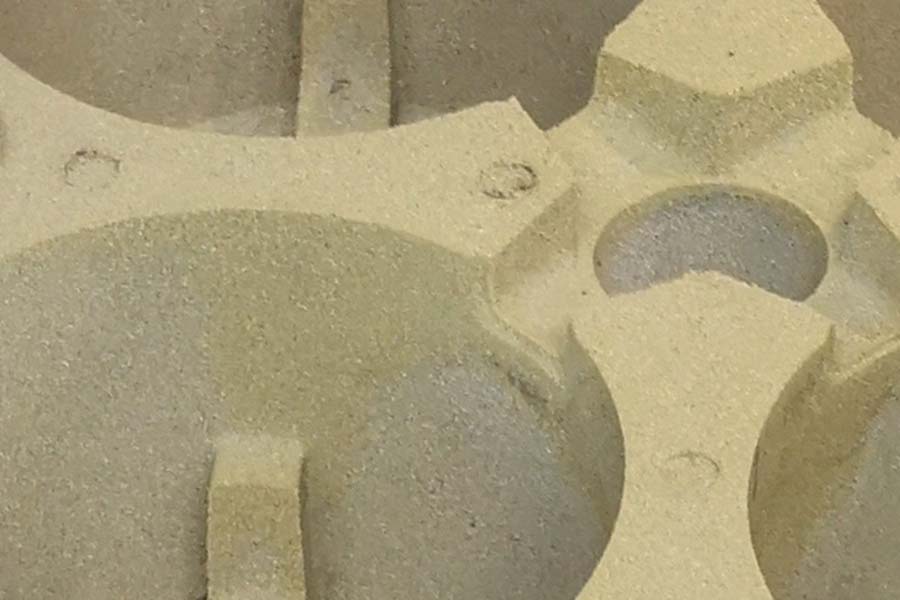
ഷെൽ മോൾഡ് കാസ്റ്റിംഗ് പ്രക്രിയയുടെ പ്രയോജനങ്ങൾ
1.ഷെൽ-അച്ചിൽ കാസ്റ്റിംഗുകൾമണൽ കാസ്റ്റിംഗുകളേക്കാൾ കൂടുതൽ അളവുകൾ കൃത്യമാണ്. സ്റ്റീൽ കാസ്റ്റിംഗുകൾക്കും +0 നും +0.25 മില്ലീമീറ്ററിൻ്റെ സഹിഷ്ണുത നേടാൻ കഴിയും. ചാരനിറത്തിലുള്ള കാസ്റ്റ് ഇരുമ്പ് കാസ്റ്റിംഗുകൾക്ക് 35 മി.മീഇരുമ്പ് കാസ്റ്റിംഗുകൾസാധാരണ തൊഴിൽ സാഹചര്യങ്ങളിൽ. ക്ലോസ് ടോളറൻസ്ഡ് ഷെൽ മോൾഡുകളുടെ കാര്യത്തിൽ, നിർദ്ദിഷ്ട ആപ്ലിക്കേഷനുകൾക്കായി +0.03 മുതൽ +0.13 മില്ലിമീറ്റർ വരെയുള്ള ശ്രേണിയിൽ ഇത് ലഭിക്കും.
2. ഷെൽ കാസ്റ്റിംഗിൽ സുഗമമായ ഉപരിതലം ലഭിക്കും. ഇത് പ്രാഥമികമായി നേടിയെടുക്കുന്നത് മികച്ച വലിപ്പമുള്ള ധാന്യം ഉപയോഗിച്ചാണ്. 3 മുതൽ 6 മൈക്രോൺ വരെ ക്രമത്തിലാണ് പരുക്കൻ്റെ സാധാരണ ശ്രേണി.
3. ഡ്രാഫ്റ്റ് കോണുകൾ, ഇവയെക്കാൾ താഴ്ന്നതാണ് മണൽ കാസ്റ്റിംഗുകൾ, ഷെൽ അച്ചുകളിൽ ആവശ്യമാണ്. ഡ്രാഫ്റ്റ് ആംഗിളുകളിലെ കുറവ് 50 മുതൽ 75% വരെയാകാം, ഇത് മെറ്റീരിയൽ ചെലവുകളും തുടർന്നുള്ള മെഷീനിംഗ് ചെലവുകളും ഗണ്യമായി ലാഭിക്കുന്നു.
4. ചിലപ്പോൾ, ഷെൽ മോൾഡിംഗിൽ പ്രത്യേക കോറുകൾ ഇല്ലാതായേക്കാം. മണലിന് ഉയർന്ന ശക്തി ഉള്ളതിനാൽ, ഷെൽ കോറുകൾ ഉപയോഗിച്ച് നേരിട്ട് ആന്തരിക അറകൾ രൂപപ്പെടാൻ കഴിയുന്ന തരത്തിൽ പൂപ്പൽ രൂപകൽപ്പന ചെയ്യാൻ കഴിയും.
5. കൂടാതെ, മോൾഡിംഗിനായി ഉപയോഗിക്കുന്ന മണലിൻ്റെ ഉയർന്ന ശക്തി കാരണം എയർ-കൂൾഡ് സിലിണ്ടർ ഹെഡുകളുടെ തരം വളരെ നേർത്ത ഭാഗങ്ങൾ (0.25 മില്ലിമീറ്റർ വരെ) ഷെൽ മോൾഡിംഗ് വഴി എളുപ്പത്തിൽ നിർമ്മിക്കാൻ കഴിയും.
6. ഷെല്ലിൻ്റെ പെർമാസബിലിറ്റി ഉയർന്നതാണ്, അതിനാൽ വാതക ഉൾപ്പെടുത്തലുകളൊന്നും സംഭവിക്കുന്നില്ല.
7. വളരെ ചെറിയ അളവിൽ മണൽ ഉപയോഗിക്കേണ്ടതുണ്ട്.
8. ഷെൽ മോൾഡിംഗിൽ ഉൾപ്പെട്ടിരിക്കുന്ന ലളിതമായ പ്രോസസ്സിംഗ് കാരണം യന്ത്രവൽക്കരണം എളുപ്പത്തിൽ സാധ്യമാണ്.
ഷെൽ മോൾഡ് കാസ്റ്റിംഗ് പ്രക്രിയയുടെ പരിമിതികൾ
1. പാറ്റേണുകൾ വളരെ ചെലവേറിയതാണ്, അതിനാൽ വലിയ തോതിലുള്ള ഉൽപാദനത്തിൽ ഉപയോഗിച്ചാൽ മാത്രമേ ലാഭകരമാകൂ. ഒരു സാധാരണ ആപ്ലിക്കേഷനിൽ, ഉയർന്ന പാറ്റേൺ ചെലവ് കാരണം, ആവശ്യമുള്ള ഔട്ട്പുട്ട് 15000 കഷണങ്ങൾക്ക് മുകളിലാണെങ്കിൽ, മണൽ മോൾഡിംഗിനെക്കാൾ ഷെൽ മോൾഡിംഗ് ലാഭകരമാണ്.
2. ഷെൽ മോൾഡിംഗ് വഴി ലഭിക്കുന്ന കാസ്റ്റിംഗിൻ്റെ വലിപ്പം പരിമിതമാണ്. സാധാരണയായി, 200 കിലോ വരെ ഭാരമുള്ള കാസ്റ്റിംഗുകൾ നിർമ്മിക്കാം, ചെറിയ അളവിൽ, 450 കിലോ വരെ ഭാരമുള്ള കാസ്റ്റിംഗുകൾ നിർമ്മിക്കുന്നു.
3. വളരെ സങ്കീർണ്ണമായ രൂപങ്ങൾ ലഭിക്കില്ല.
4. ചൂടാക്കിയ ലോഹ പാറ്റേണുകൾക്ക് ആവശ്യമായ ഷെൽ മോൾഡിംഗുകൾ കൈകാര്യം ചെയ്യുന്നതിന് കൂടുതൽ സങ്കീർണ്ണമായ ഉപകരണങ്ങൾ ആവശ്യമാണ്.
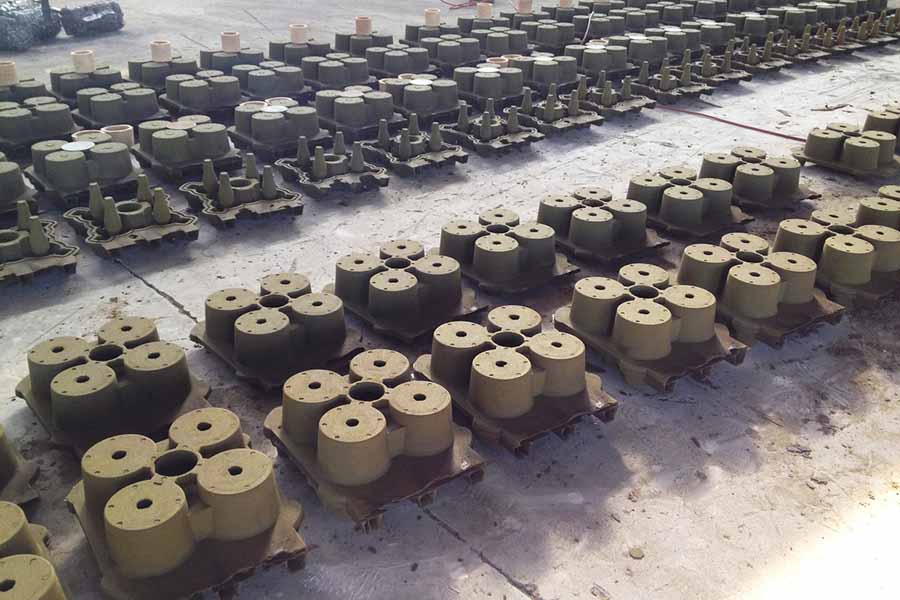
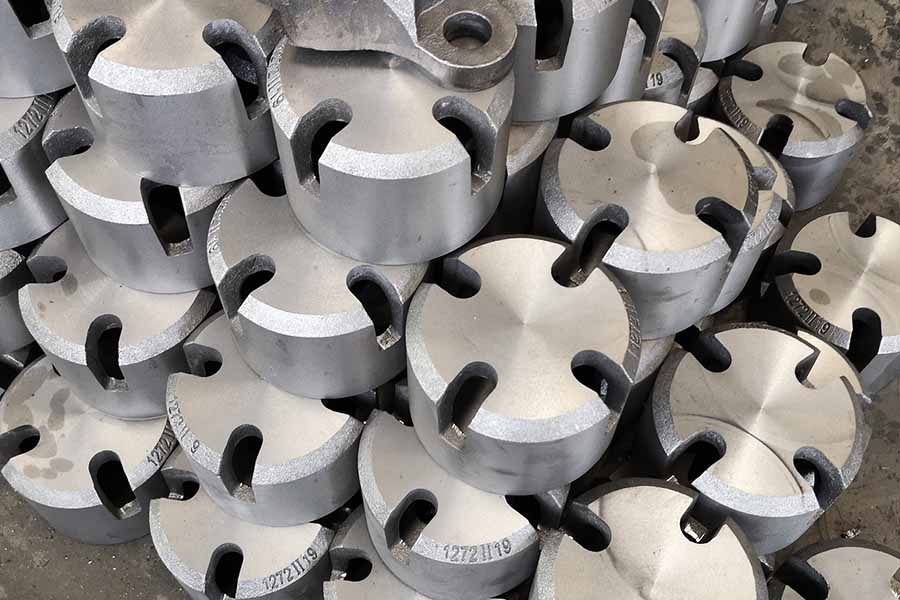
പോസ്റ്റ് സമയം: ഡിസംബർ-25-2020